This is the initial report stating the profile of the artisans in Guatemala that Irene Cajas and I are working for this semester. Thanks, Irene, for the awesome work!
PDDW: Team SHOES 2009
CONTACT INFORMATION
Calzado Rogal Legend Boots
Orlando Galdamez (502) 5144-3826
Oscar Galdamez (502) 4311-7399
Arnulfo Galdamez
The company specializes in the manufacture of shoes and other leather products, such as aprons and bags. Most of their production consists of manufacturing industrial shoes for large factories in Guatemala.
HISTORY
The company started when Arnulfo´s dad started working in the shoe business, adding the soles to the shoes in Antigua, Chimaltenango; he had learned the trade from his brother. After some time Arnulfo´s mother (Maria Tejeda) decided to expand the business by taking out a line of credit from a bank and began producing handmade shoes. It was Maria who began commercializing the products; after she got sick it was Arnulfo who carried on the business, the only problem where the debts with the furrier. Arnulfo learned the tricks of the trade and kept the family business running while paying off the debts. He also figured it was better to buy directly from the furriers, which reduced his costs and debt in the long term.
As his family grew Arnulfo taught his children Oscar and Orlando how to work in the family business. Over the years the business grew in Antigua and they employed around 47 people who worked in the manufacture of shoes, however the company suffered a downfall when while working with a Mexican company the economy in Mexico took a wrong turn and caused major loses to the company. As a result they had to sell their property in Antigua and relocate to Pastores (a town known for their shoe and leather product manufacture) and later to Parramos, both town merely 20 minutes away from Antigua.
With the changing history, the company has undergone some brand changes as well. It was originally called INCALGA (Industrias de Calzados Galdamez), however the name was changed after they encountered some problems with the social security in Guatemala or IGSS (Instituto Guatemalteco de Seguridad Social). They closed the company and reopened it with the name INBOSA (Industria de Botas S.A.), the new company only employed members of the family and did not declare taxes. They say that some of the biggest challenges they face in the country to grow as a company is the taxation levels implemented by the government, the high interest rates of loans in banks and the government itself. Another challenge they face is the inability to compete against large local companies such as GRUPO COBAN a shoe manufacturer in the country with a huge production and marketing capacity.
Almost 30 years ago the shoe manufacturers in Pastores, tried to create an association. The initiative was the work of Arnulfo who tried to unite all the manufacturers in the hopes of helping each other out and creating better opportunities for themselves, however it was the small producers the ones that lost and got no benefits from the association. It was 12 years ago that a cooperative surfaced in Pastores, unfortunately the money they managed was all lost due to the lack of a proper administration.
Back in the 1990s they worked with a shoe design that they called “Swedish Boots”. This turned out to be a huge success especially in the United States and Mexico. They worked with a Mexican resident in the USA called Guillermo Vargas who lived in LA; the partnership was a successful one until they burned Mr. Vargas shop down.
SHOE MANUFACTURING PROCESS
The pattern for the shoe is drawn out in cardboard and cut. If the production for that specific model is a large one, then they take the patterns and make the metal die cutters. The patterns for the shoes are all taken from the shoe lasts and shoetrees, according to the different shoe sizes.
The molds are used to cut the leather needed to make each shoe. Some are hand cut while other are cut using the die cutters and a press.
Once the leather parts have been cut, they are worn off around the edges so they can be either glued or sewn easily.
The worn off edges are glued by hand using a small hammer.
All the parts are sewed together with a double or triple stitch depending on the shoe type and material. The necessary components to make the collar of the shoes are added and sewed with the leather.
The lining is added and glued to the inside of the shoes. This gives the shoe its form and rigidity. This used to be glued with yuca starch, later they started mixing rubber with gasoline which in time created glue used to put all the parts together, however this was highly flammable and volatile.
The sole is anchored to the shoetree using nails to keep it in place. It is then joined to the playrip which makes the shoes waterproof.
If the shoe needs a steel toe, it is joined to the upper leather part of the shoe using glue. Some of the steel or plastic toes have tabs which help make the shoe more resistant and durable. If the toe has a tab it takes twice the time for the shoe to be fitted on the shoetree.
After the excess leather is removed, while on the shoe tree, the PVD edge is glued and then sewed using the “Good Year Welt” system. Before it used to be done by hand.
The inner sole is glued using polyurethane glue heating the inner sole and shoe and then joining both. This process takes between 10 to 15 seconds per shoe pair. After the innersole has been glued and all the excess removed, it is stitched with a plastic thread and then the sole is polished.
The same method is used to glue the sole of the shoe.
They have very little waste of material, and they try to make the most out of all the leather parts they use. They usually work only in brown and black leather, which is the easiest material to find in the country and the easiest to sell as well. They are able to produce up to 300 pairs of shoes a day. The cost of a shoetree is Q. 150.00 and this cost has to be covered in one season.
PACKAGING AND TRANSPORTATION
The packaging of the finished products often consists of transparent plastic bags or brown cardboard boxes. They lack proper packaging that identifies the company, brand, shoe size, color and any other important information the costumer might need. The cost of the plastic bags is about Q. 0.35, and the boxes depend on the size but they can range from Q. 1.35 to Q. 5.00.
They usually do the transportation and distribution of their products in pickup trucks, taking their products to the different selling points. Some of the larger companies for which they work will sometimes go to their shop to pick the products up.
PRIME MATERIAL
Most of their prime material they use for the manufacture of the shoes is all bought in Guatemala City at the furrier’s. They travel twice a week or whichever times are needed depending on the availability of the material and their needs at the shop. Most exotic skins are imported but there is also national leather.
The leather is sold by the square feet and the price depends on the animal it comes from and the color and quality. They also used recycled leather from the leather jackets that come from the USA and are sold at the goodwill stores in the country. These are relatively cheap (from Q.30.00 to Q. 60.00) and can be used to make certain parts of the shoes and boots.
COMPANIES THEY WORK FOR
Z Gas: this is a local gas company they work for producing 400 industrial shoes twice a year.
Caravari: this is a company from Argentina and they produce leather boots and aprons for them. They work using a system of catalogue in which they have a sample of the type of shoe, style and material, the same sample the company has in Argentina, so making the orders is easier for them.
PROTOTYPING
The costs of prototyping are usually 50% - 50%. If the production of the shoes is a large one they will assume the cost of the prototypes entirely. The amount of time it takes to manufacture a prototype depends on many things; one of them is the shoetree, if they need a new one, the production of it alone takes 15 days, if they already have the shoetree and the material they are to be working with it takes them 8 days.
BRAINSTORMING
- Create a product line (belts, bags, shoes, accessories)
- Diversify the companies products
- Create a marketing plan
- Develop a brand (branding)
- Combining different materials (microfiber, fabric, natural fibers)
- Creating a website for their products
- New packaging and transportation solutions
- Tailoring (custom made products which can be adapted to the consumers needs and wants)
Wednesday, September 16, 2009
Saturday, September 5, 2009
The FAIR WINDS TRADING inc. developing country trade example...
There is a company called Fair Winds Trading, which I found out about as I was sitting at the Starbucks one morning reading my paper and having my morning coffee. There was a stand right in front of the cash register and it had a bunch of tumblers on display. The tumblers had unique textile inserts of African patterns made by African artisans in Africa. It was clearly stated on the brochures on the stand that the profits made from the sale of each tumbler went, in percentage, right back to that same set of artisans that had manufactured the cloth.
They were unique and it was an interesting way of introducing a characteristic artisan good from a faraway land to a richer American market.
I think that, at the very least, this should be taken into consideration as a case study, and, perhaps, there should be a dialogue with Fair Winds trading with regards to establishing relationships with Guatemalan manufacturers.
I think they currently work only with North African artisans.
Here is an excerp from their website...
"Fairwinds Trading is a for-profit company that uses business as a strategy for economic empowerment of people, especially women, in the Majority World. The Majority World is where two billion of the world’s three billion people live, in poverty. Our focus on women as a preferred partner is based in part on our history, in part on our leadership as a woman-owned firm, and in part on evidence that raising the standard of living for women has the greatest positive multiplier effect within families, communities and cultures.
The company’s philosophy and business model embody a new paradigm for global economic empowerment. They recognize that compassionate aid, needed in moments of crisis, becomes culturally destructive if continued too long. They demonstrate that cross-cultural business partnerships, rooted in mutual learning and growth, can bring sustainable economic power to women around the world.
Our mission is to connect cultures through business, art and understanding."
The company’s philosophy and business model embody a new paradigm for global economic empowerment. They recognize that compassionate aid, needed in moments of crisis, becomes culturally destructive if continued too long. They demonstrate that cross-cultural business partnerships, rooted in mutual learning and growth, can bring sustainable economic power to women around the world.
Our mission is to connect cultures through business, art and understanding."
Here is the link and here are a couple of photographs...
Friday, September 4, 2009
Alternative/Repurpoused Materials in Fashion
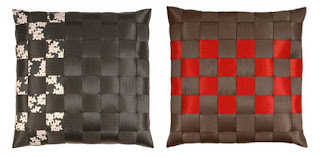
There are a bunch of cool sites I found that follow devcloping trends in the use of repurpoused or unconventional materials in the creation of the latest fashions. One of the most extensive at tracking these trends is INHABITAT. It has sections devoted to various aspects of design, from Architecture to Accessories to Transportation. Cool stuff and useful as a tracking device...
The picture on the top is of a couple of pillows made from repurpoused seatbelts from TING London. Its just one of the cool products I found on the site.
The site Suite101.com has alot of interesting information on how to go about repurposing old clothing, taking it apart, and making newer stuff from it, stuff which has the potential to create new trends.
The site TreeHugger.com is cool as a general site to follow up on how to be green, think green, and buy green. It is not necessarily specifically about repurposing materials, but it is a great launch pad for research into green related topics. It has alot of good information and some very interesting original content articles
Finally the blog COOLHUNTING Green is cool in terms of informing us about one off or limited production furniture pieces and other wearable and non wearable accessories. As I learn more about it I will keep informing the blog...
Organizations for distributions of Shoes to the Poor
Shoes for Humanity
The pipeline is a partnership of people and organizations whose code of ethics and social practices guide them to make a voluntary contribution of resources toward the betterment of humanity. It delivers free recycled shoes to those areas of the world where there is great human suffering due to extreme poverty. The initial pipeline carries recycled sandals from America to East Africa.
http://shoesforhumanity.org/
Souls4Soles
Soles4Souls facilitates the donations of shoes, which are used to aid the hurting worldwide. Shoe companies, retailers, and individuals can donate footwear (both new and used). Soles4Souls is a 501(c)(3) recognized by the IRS, and donating parties are eligible for tax advantages.
The idea behind gifts of shoes is nothing new to the Soles4Souls team, as they coordinated relief efforts for the Asian Tsunami and Hurricanes Katrina and Rita, netting over 1 Million pairs donated for these disasters. The team originally operated as www.katrinashoes.org with several churches partnering in the collection and distribution of footwear.
http://www.soles4souls.org/about/
http://soles4souls.blogspot.com/
The pipeline is a partnership of people and organizations whose code of ethics and social practices guide them to make a voluntary contribution of resources toward the betterment of humanity. It delivers free recycled shoes to those areas of the world where there is great human suffering due to extreme poverty. The initial pipeline carries recycled sandals from America to East Africa.
http://shoesforhumanity.org/
Souls4Soles
Soles4Souls facilitates the donations of shoes, which are used to aid the hurting worldwide. Shoe companies, retailers, and individuals can donate footwear (both new and used). Soles4Souls is a 501(c)(3) recognized by the IRS, and donating parties are eligible for tax advantages.
The idea behind gifts of shoes is nothing new to the Soles4Souls team, as they coordinated relief efforts for the Asian Tsunami and Hurricanes Katrina and Rita, netting over 1 Million pairs donated for these disasters. The team originally operated as www.katrinashoes.org with several churches partnering in the collection and distribution of footwear.
http://www.soles4souls.org/about/
http://soles4souls.blogspot.com/
The Toms Shoes Example
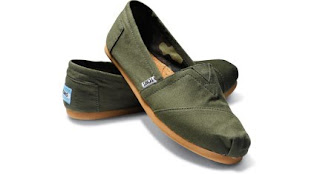
This is a link to the website for Toms Shoes. Toms Shoes is a company started by Blake Mycoski
after a trip he took down to Argentina, where he saw a very characteristic shoe type worn by local farming villagers (algaparta), and became inspired to start a company that manufactures variants of this particular design.
At the same time as the founding of his for profit company in the US, he also started a non profit arm of Toms which gives one pair of shoes to a child in need in a variety of countries for every pair sold in the Profit arm of the company.
The shoes are also sustainably manufactured and the company has won numerous awards for its philantropic efforts.
This is a picture of one of their shoes. The design seldom varies but the fabric pattern and colors vary greatly...
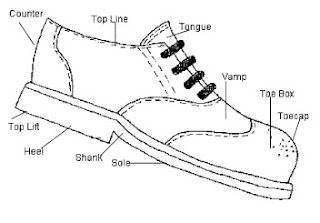
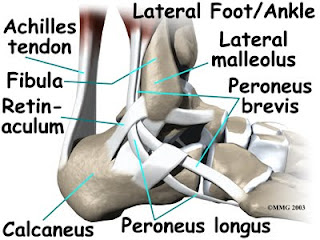
This is a series of links that Ive been looking at in order to try and figure out what is known about the proper ergonomics and anatomy of a shoe.
The first link is about Ergonomics in general. It is a wikipedia link and its pretty compresensive
The next link is about the history of western shoe design from the late reniassance on to the 2000's. It doesnt have much information in the way of pictures, but it looked like it would be a good starting point for some exploration and clues on various types of shoes through history
This link I thought would be good to check out for the basic anatomy of a human foot.
and here are some images of the human foot anatomy just for our information
Subscribe to:
Posts (Atom)